We are all witnessing the current data explosion: social media data, clinical data, system data, CRM data, web data, and lately tons of sensor data! With the advent of the Internet of Things, system and monitoring applications are producing humongous amounts of data, which undergo evaluation for a variety of reasons, for example to optimize costs and benefits, predict future events, classify behaviors, implement quality control, etc. All these use cases are relatively well established by now: a goal is defined, a target class is selected, a model is trained to recognize/predict the target, and the same model is applied to new never-seen-before productive data.
The newest challenge now lies in predicting the “unknown”, i.e. an anomaly. An anomaly is an event that is not part of the system’s past; an event that cannot be found in the system’s historical data. In the case of network data, an anomaly can be an intrusion, in medicine a sudden pathological status, in sales or credit card businesses a fraudulent payment, and, finally, in machinery a mechanical piece breakdown.
In the manufacturing industry, the goal is to keep a mechanical piece working as long as possible – mechanical pieces are expensive – and at the same time to predict its breaking point before it actually occurs – a machine break often triggers a chain reaction of expensive damages. Therefore, a high value is usually associated with the early discovery, warning, prediction, and/or prevention of anomalies. Specifically, the prediction of “unknown” disruptive events in the field of mechanical maintenance takes the name of “anomaly detection”.
The problem here is: how can we predict something we have never seen, an event that is not in the historical data? This requires a shift in the analytics perspective! If data describing normal functioning is what we have, then normal functioning we will predict!
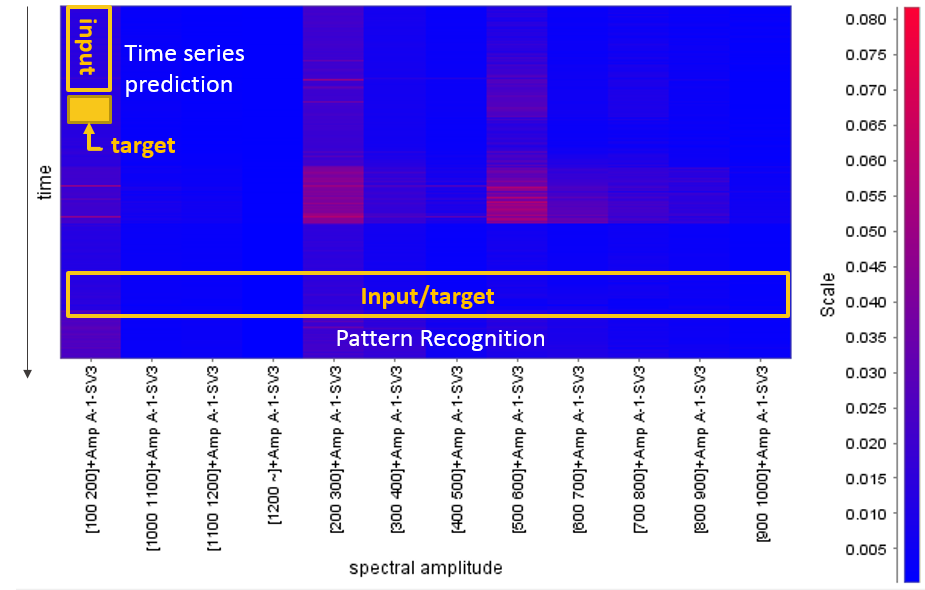
Pre-processing: Standardization and Time Alignment
For this project, we worked on FFT pre-processed sensor data from 28 sensors monitoring a working rotor. The FFT transform produces a matrix of spectral amplitudes for a time segment and a frequency value.
In order to standardize the time and frequency references, frequency values were binned into 100Hz-wide bands and time values were binned into dates. The FFT spectral amplitudes were then averaged across each date and each frequency bin. Cells in the final FFT matrix refer to one single date and one single frequency band for a single sensor. Considering all sensors, we get 313 FFT spectral amplitude columns in total.
After this standardization task, a time alignment was performed, inserting missing cell values where no date was available. The final FFT matrix has dates on one axis, frequency bins on the other axis, and average spectral amplitudes as cell values, with occasional missing values.
This kind of FFT matrix can be observed from two different perspectives (Fig. 1):
-
A vector of spectral amplitudes across frequency bands evolving over time
-
A time series of spectral amplitudes on a single frequency band
Different approaches for anomaly detection can be implemented depending on which one of the two perspectives we decide to adopt. The philosophy, however, remains the same: learning to predict normal functioning, to trigger an alarm when predictions are failing!
Predicting Anomalies using Time Series Analysis
We used both perspectives to identify anomalies: time series and vectors across frequencies. Here, however, we describe only the time series related approach. The pattern recognition related approach is a topic for a future post.
As our data set contains only data to describe the normal functioning of the rotor, we use these data to predict anomaly-free measure values and we measure whether such a prediction is good enough. If it is not, we can assume we are out of the range of “normal functioning” and we can trigger an inspection alarm.
The more accurate the prediction model for the normal functioning signal, the more precise and more robust the consequent alarm is that is triggered. With this goal, an auto-regressive (AR) model is trained on an anomaly-free time window using 10 past history samples on each one of the 313 spectral amplitude time series. Some boundaries of normal functioning values are then defined around the average prediction error observed in training.
During deployment on new data, if the prediction error diverts from these boundaries, an alarm is triggered to alert that is time to inspect the machinery.
Deployment and Optimization
Because the AR models have been trained over a time window of normal functioning, they can predict the next measure only for a correctly working rotor. Most models will actually fail at predicting the next measure, if the rotor functioning has already started to change.
During deployment:
-
the AR models are applied to productive data to predict the next value
-
the distance error is calculated between the original next value and the predicted next value
-
this distance error is compared with the boundary defined on the training window:
IF (distance * distance) > boundary THEN alarm = distance
This generates 313 “alarm” time series. Due to temporary inabilities of the models to match the real values with the predictions, random spikes can arise in the “alarm” time series. To make the alarm system more reliable, we use a two-level structure: this first alarm, the one defined above, is merely a warning signal and is processed again to produce a more accurate second level alarm signal. Using a Moving Aggregation node, the moving averages are calculated on a backward window of 21 samples of the level 1 alarm (warning) signals. This moving average operation smooths out all short random peaks in the level 1 alarm time series, retaining only the ones that persist over time.
Figure 2 shows a stacked plot of the 2nd level alarm time series, obtained with an R View node. Here the early signs of the rotor breakdown – which occurred on July 22 2008 - can be tracked back as early as March 2008 ‒ if using a sensitive threshold, or as early as May 2008 ‒ if using a threshold that is not so sensitive.
Summing up all 313 alarm values across the frequency bands and referring to the same date naturally improves the system performance, in terms of both specificity and sensitivity. An optimization loop, maximizing the trigger accuracy, can also help to define the optimal threshold on the 2nd level alarm time series.
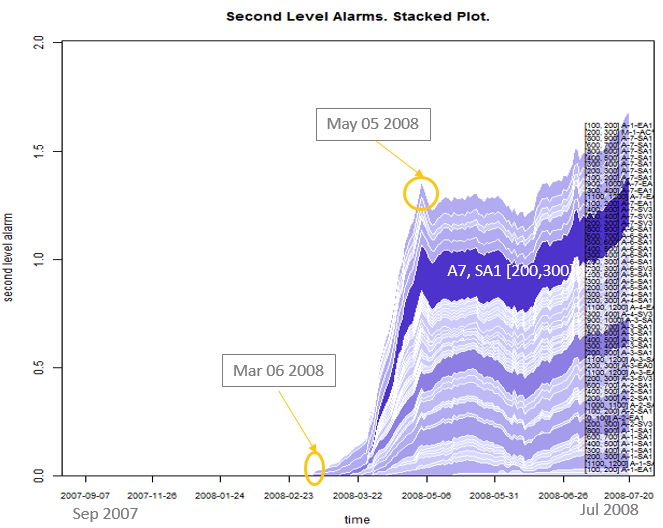
Once the models and alarm criteria are in place, the final part of the deployment workflow needs to take action, if needed. Many possible consequent actions can be started and controlled from within a KNIME workflow through a specific node or just a general REST interface: e.g. howling sirens, system switch-off, or just sending an email to the employee who is in charge of mechanical checkups. In our deployment workflow, the designed action consists of sending an email. The 2nd level alarm value is then transformed into a flow variable that triggers the output port of a CASE Switch node connected to a Send Email node.
Whitepapers and Workflows
The final workflow, named “Time Series AR Deployment”, is shown in Figure 3. There you can see the metanode that generates the 1st level alarms, the metanode that generates the 2nd level alarms, and the metanode that takes action named “Fire if Level 2 Alarm”. Workflows and data used for this study can be found on the KNIME EXAMPLES Server under 050_Applications/050017_AnomalyDetection/Time Series Analysis.
The whitepapers, describing the full details of this implementation, can be downloaded from https://www.knime.org/files/knime_anomaly_detection_visualization.pdf (for the pre-processing part) and from https://www.knime.org/files/Anomaly_Detection_Time_Series_final.pdf (for the time series analysis part).
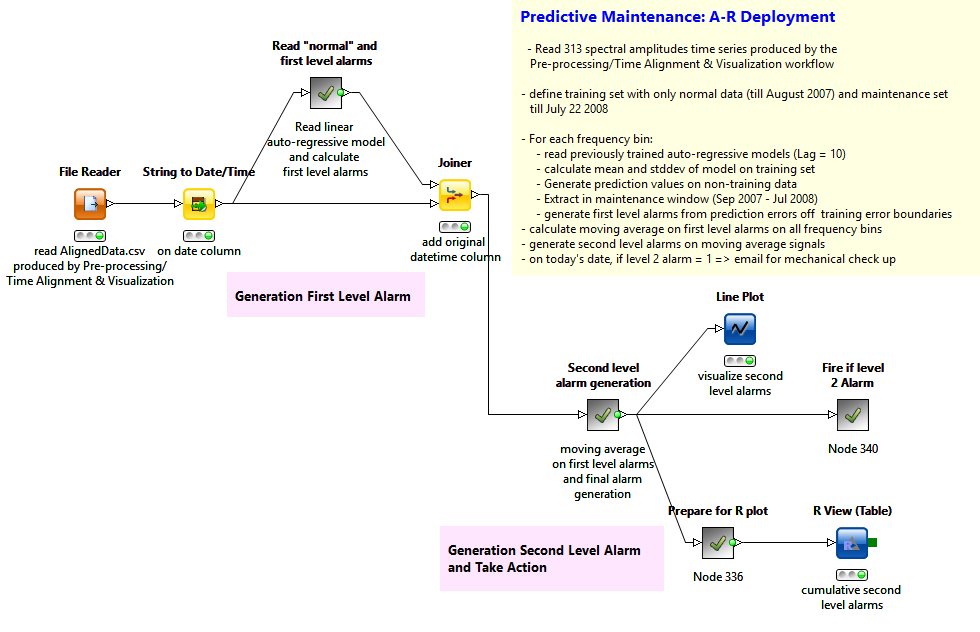